Forefront | Blog
Reconsidering a J.I.T. Strategy – The Hidden Costs of Inventory
During a supply chain crisis, companies often question the wisdom of continuing a Just-In-Time (J.I.T) materials strategy, and with good reason. Supply chain horror stories have surfaced over the past year regarding supplier facilities being closed for weeks on end due to the pandemic, or labor shortages causing force majeure. Pictures of record numbers of ships sitting offshore without being able to unload appear on the nightly news. Stressful conversations occur daily as purchasing departments literally beg for product from alternate suppliers; and then due to different delivery routes, pay multiple times the normal cost of transportation.
All the topics stated above are reason to be concerned about not keeping materials on hand, let alone thought of shutting down and or losing a major customer. By sharpening a pencil, most companies can calculate what this supply chain crisis has cost them. Several tactics can be employed to reduce the risk of repeating these kinds of emergencies…
• Focus on material resource planning
• Find primary AND secondary vendors to ensure continuity of supply
• Negotiate with transportation carriers
• Tighten internal operations to reduce attrition/defect rates is crucial for continued success.
But, if carrying additional inventory becomes part of the supply chain strategy, be aware that inventory comes with carrying costs. Carrying costs are the costs to hold, store, and handle inventory. The rule of thumb for cost of carrying inventory is 25% of the average annual value of that inventory. Meaning for every $1 million of inventory carried, it could cost $250,000 to keep it on hand.
So, how is that possible? The table below does a good job explaining. Companies often need to use a line of credit to purchase additional inventory, and then the funds are not available for use in something that could be driving additional profits. Inventory typically needs to be insured. More warehouse space, heat, light, and power may be required. Additional warehouse labor and equipment such as forklifts may be necessary. Of course, administrative tasks such as record keeping, and inventory counts add cost. Finally, the risk of obsolescence may increase as higher levels of inventory are carried depending on the effectiveness of a company’s inventory management system/process.
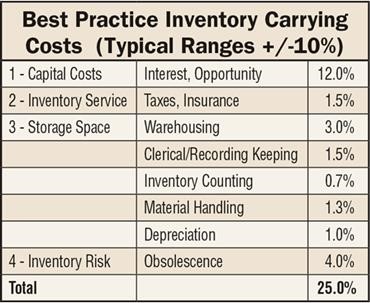
Each company’s situation is different and inventory carrying costs will vary. Its important to keep in mind that a company may be able to pass these costs on to customers when pricing its products. Just as the company itself is interested in continuity of supply, and willing to pay a premium, so might be its customers. Regardless, weighing the cost of a supply chain crisis against the cost of increased inventory levels is a good idea prior to a decision. O’Keefe’s professionals will help you to analyze and implement effective strategic supply chain management systems and processes for sustained success.